The role played by surface coating systems on thread tapping screws
29 July 2019
Thread tapping screws are in frequent use, particularly in lightweight construction. To ensure process reliability during assembly and to create a reliable component, at the design stage of the fastening - besides the actual design of the screw - the surface coating system must also be precisely defined.
Thread tapping screws are screws that form their thread as they are screwed into a pre-drilled or cast corehole, by chiplessly creating a specially shaped threaded end. In this way they perform as a tightly-connected fastener with the additional function of a positive-locking captive fastening. The screws are driven into through-holes, and very often also into cast coreholes in die-cast aluminium and sometimes in die-cast magnesium or zinc too.
To ensure reliable assembly in practice, technical experts refer to DIN 267 Part 30. This standard defines the mechanical characteristics of strength class 10.9 metric thread tapping screws. Characteristics include the minimum breaking torque, and the driving and tapping torques into the specially provided test templates with their precisely defined bore holes and tension failure forces. Furthermore, the standard also defines the screw's tapping zone. It also sets out the ratio to and compatibility with the metric screw. This means that the tapped female thread must be able to accept a standard metric screw.
Good tapping performance with the trilobular thread cross-section
In addition to the DIN standard there are special company standards, such as those issued by Magna, Ford, the BMW Group or Bosch. These often set out even higher specifications for certain applications. To be able to respond to these requirements as a supplier, we need to be in possession of full and accurate details of the screw fastening.
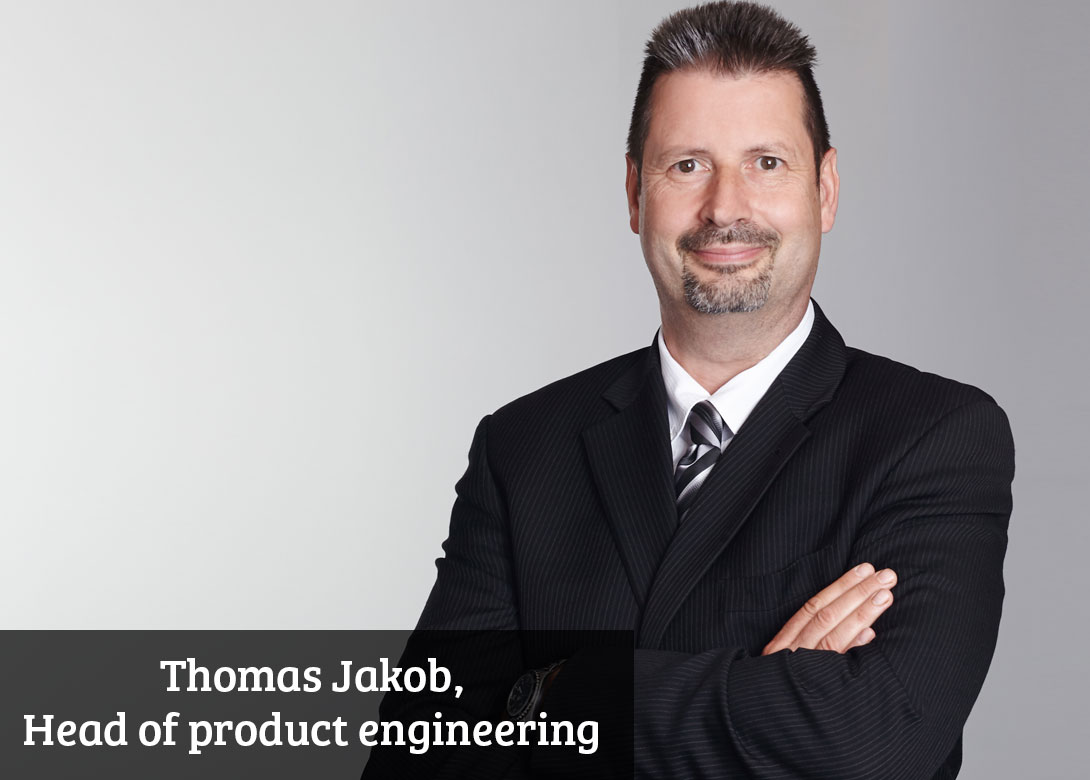
Thomas Jakob is the head of product engineering at Arnold Umformtechnik GmbH & Co. KG in Forchtenberg. He is fully aware of customers' requirements as well as the fastening solutions available to implement them. "Thread-tapping screws are primarily used in lightweight metals. In this respect the TAPTITE 2000®, the latest product from the TAPTITE® range, demonstrates excellent tapping performance. It is distinctive for its radial profile which makes it easier for the nut material to flow in the direction of the thread core. There is therefore less friction and a lower tapping torque," explained Jakob.
The trilobular TAPTITE screw has been on the market for over 30 years. The principal aim of this trilobular, slightly triangular cross-section is to reduce the tapping torques to ensure stable assembly. The aim here is to achieve a wide difference between the tapping and the tightening torque, as well as a sufficient gap between the tightening torque and the failure torque (overturn torque or screw fracture).
Thread tapping screws can be used in a wide range of applications. They are often used in lightweight metal applications - aluminium or die-cast aluminium, other lightweight metals, and die-cast magnesium - but they can also be used in solid steel screw fastenings. Examples of applications for thread-tapping screws are to fasten gears and sensors, fasteners used in the engine compartment, fixing plates, actuators and pumps.
Defining the perfect coating and lubricant
However, where the customer's requirements are higher than the DIN standard, requiring even lower tapping torques, the coating system also has a role to play. A base coating is generally applied to the surface of the screw, intended to protect against corrosion. Usually this is a zinc, zinc-nickel or zinc flake coating.
"OEMs have their specifications for surface coatings, which generally refer to the base coating and corrosion protection. We then use them to define the low-friction coating that is required for the screw. This is important when creating a design that is oriented towards preloading to join metal components," said Jakob.
When it comes to coating systems there are VDA guide values referenced to corrosion protection and the friction coefficients of metric screws. However these cannot be transferred directly for use on thread-tapping screws, but must be used as guidelines. Low-friction coating is generally supplementary to this - and is also relevant to the function of thread-tapping screws. DIN 267, Part 30 explicitly refers to this.
It is important that the entire coating system and the component match one another exactly, i.e. the geometry of the screw must match the counterpart with optimum precision. In addition, the base coating and the corrosion protection requirements must be implemented correspondingly. As a rule this is generally achieved with a zinc, zinc-nickel or zinc flake coating.
"The whole interacting coating system is important for the preload force - the base and anti-friction coating as well as the seal," stressed Jakob.
Coating covers many challenges
The experts at Arnold have achieved good results with a TAPTITE 2000® and a zinc-flake coating plus sealant plus anti-friction coating. "We examined very many coating systems and on this basis can make specific recommendations for implementation in various applications. We also looked carefully at technical cleanliness and discovered that the cleaning processes can often have undesirable effects on the coating system, because some of the lubricant and seal is abraded during the process," said Jakob.
A further challenge is posed by very small screws smaller than M6 with high corrosion resistance requirements. In such cases, zinc-nickel is often used as the coating, because it is more suitable for any onward processing. However, it sometimes makes the tapping process more difficult.
Defining the pre-load force requires a high-level of technical expertise. While the requirements and calculation methods used to define the preload force in metric screws are clearly defined, in tapping screws, the specifications merely specify the test plate and the tapping torque in the test plate.
It is important to agree the details with the customer
In order to implement a cost optimised screw fastening directly into metal for the customer's particular application, the experts at Arnold work closely together with the customer. In doing so they note a whole series of key data. The first thing is to check whether a thread-tapping screw can be used at all for the fastening in question, bearing in mind the necessary preload forces. A further point to check is of course the amount of installation space available, and the associated achievable penetration depth. Arnold is then able to make the relevant recommendations, depending on the application that is planned.
"Particularly for lightweight metals, the corehole bores are often already pre-cast. Here, we make recommendations of how the corehole should look and the tolerances that must be taken into account. But ultimately it is the client in the frontline who needs to agree with the foundry whether the solution they are thinking of is appropriate for casting," said Thomas Jakob highlighting a further aspect.
The specific operating situation for the component also plays a role, i.e. operating loads and temperatures. And of course we need to take account of whether the manufacturer imposes certain assembly specifications for the component.
Moreover, many companies have their own factory standards that must be observed, particularly as regards overturn, tightening and tapping torques. The strength class, the design of the head and the thread also have a part to play in this respect. "By carrying out the relevant tests in our Fastener Testing Center we are very often able to help our customer with screw fastening analyses using the original component, in order to define the optimum tightening torque, so that when our customer goes into series production we can ensure a perfect assembly operation," continued Jakob.
In principle, guide values exist for the design of screw fastenings in order to generate process reliability during assembly. At Arnold, moreover, a number of tools assist with problems such as the design of the coreholes, and the Fast Creator helps with the design of the screw itself. Currently in development is a tool that can be used to make well grounded recommendations relating to the torque-preload force behaviour of perfectly tailored thread-tapping TAPTITE 2000® screws.
Thought is also given to any possible repairs. "When the screw fastening is first made, it is unlikely that thread-tapping screws would ever come loose by themselves. In the event of a repeat screw-fastening, or if a repair needs to be made, the entire surface coating system should be checked again to ensure that the fastening is secure," said Jakob, explaining once again the complexity of a fastening solution. If required, customers can arrange an analysis of their repair concept at the Forchtenberg Testing Centre, using the original components.
Regardless of the application that the thread tapping screws are destined for, to ensure a reliable fastening solution an accurate preliminary analysis is just as important as a perfectly designed surface coating system.