GESIPA UK: Encouraging the next generation
26 May 2016
Established as a UK subsidiary for the German GESIPA Group in 1972, GESIPA Blind Riveting Systems Ltd (GESIPA UK) has grown to become the Group’s technical centre of excellence for threaded fasteners. Claire Edwards, deputy editor, visited the Keighley operations to find out more about GESIPA UK’s manufacturing capabilities and how it is encouraging the next generation of fastener professionals.
Hanging in the corridor leading to GESIPA UK’s factory is a photo frame containing a sample of every different threaded fastener produced at the Keighley site over three decades. “Every time a customer comes to visit they’re always impressed at what we’ve produced on-site,” explains Diana Scholefield, managing director at GESIPA UK. “Our products are ‘Made in the UK’ and we’re proud to shout about it. It may be a cliché, but at GESIPA UK it is not just a simple rivet or rivet nut.”
A thorough understanding of the products is something Diana – a qualified mechanical engineer – is keen to install in all her employees. Having joined the company as a project engineer, and progressed to both quality and operations manager before being made managing director in 2014, Diana has first-hand experience in almost every aspect of the company. “Quality is key. We pride ourselves on the high-quality of our products and have the technical expertise within the company to deliver a fast, reliable service,” mentions Diana.
This technical expertise led to GESIPA UK becoming the technical centre of excellence for threaded fasteners within the Group. This means the Keighley site now supplies its entire threaded fastener range to the Group’s worldwide customers.
The extensive threaded fastener range manufactured on the 15,340m² site – which is TS:16949 accredited – includes 430 special blind rivet nuts and 28 different varieties of rivet nut studs, all available in aluminium, steel and stainless steel in diameters M4 – M10. Also produced at the UK site is the MEGA GRIP® high strength structural blind rivet with a wide grip range.
The UK site features sales offices, an on-site quality and inspection department – including optical inspection machines and tensile testing – a warehouse with approximately 1,600 pallet locations, and a shop floor divided into ‘teams’. “The ‘teams’ enable our staff to fully understand the products they’re producing. We can offer the technical expertise our customers require and develop bespoke solutions,” says Diana. As well as its standard catalogue range, GESIPA UK also works closely with end-users to provide bespoke engineered solutions – approximately 70% of what is produced at the UK site is special fasteners.
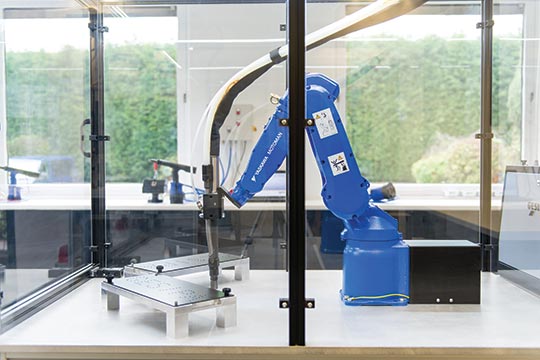
Currently, GESIPA UK manufactures 130 million threaded fasteners annually with its manufacturing facility operating seven days a week. In July, GESIPA will also take delivery of the first of three new heading machines. The new machine will join a number of thread rolling machines, assembly machines, packing machines, an on-site annealing plant for aluminium, degreasing and polishing, as well as several 5 and 6 die, 5 and 6 blow machines. Once the final heading machine is installed in December, the company will have the capacity to produce 210 million threaded fasteners and 60 million MEGA GRIP rivets annually. This will also enable GESIPA UK to grow its export capacity, which currently stands at 40%.
GESIPA UK’s biggest market for rivet nuts and rivets is the automotive market, with other important markets including the electronic and white good industries. As part of a training initiative, the company arranges for its staff to visit key customers to see its products
first-hand on the assembly line. “Visiting our key customers on-site gives our staff the opportunity to see the products they’re producing in a completely different light. When they see the end product they come back to the site full of enthusiasm and a new understanding,” comments Diana.
However, the company’s philosophy of educating and informing is not limited to its 68 employees. The UK site also includes a fully operational demonstration centre – opened in October 2014 – which it encourages potential and existing customers to visit.
“The demonstration centre enables us to prove our capabilities and the quality of our products to our customers. Actually showing the customer how a product can be used and explaining the benefits first-hand is a big advantage compared to simply telling them about the product,” explains Diana.
The demonstration centre features the GAV automatic-feed blind riveting systems for rivets; the FireRex® – robotic bind rivet nut setting unit; and also has the full range of GESIPA tools on display. The centre has enabled GESIPA to offer added value to its UK customers by providing training on its products and teaching customers how to optimise their processes and maintain their tools.
GESIPA UK also works alongside local schools and colleges to encourage young people to visit its factory and demonstration centre. “We are keen to present a vision of engineering to the local community. The next generation are deciding on their career paths and we want to make them aware that the fastener industry is a viable option for them,” adds Diana.
It’s clear from visiting the Keighley site that there is a sense of pride and loyalty at GESIPA UK, which has seen generations of families now working across all of its departments. The enthusiasm and experience the employees have is reflected in the quality of the products it is producing and is enabling the company to substantially grow its capacity.
“The fact our products are ‘Made in the UK’ means guaranteed quality and reliability. Our experts will continue to work together to produce the best quality product,” states Diana.